The Modern Battery Lab
- Updated2024-10-31
- 4 minute(s) read
The Modern Battery Lab
The Modern Battery Lab combines the advanced features of the PAtools Battery Lab Software with the power of SystemLink Enterprise to enable you to create, configure, execute, and monitor electric vehicle (EV) battery tests. The Modern Battery Lab also enables you to analyze test data on a mass scale.
The Modern Battery Lab provides engineers with the following capabilities:
- Optimization of workflows that enable collaboration between product teams, test engineers, lab managers, and operators.
- Actionable insights from data across the battery life cycle.
- Dashboards and visualizations that provide real-time feedback to stakeholders.
- An open and flexible software platform that enables fast adaptation to changing requirements.
- Coordination and test scheduling to optimize testing resources.
- Automation of data analytics and reports for post-test review.
- Connection to the most popular cyclers and instruments.
Components of a PAtools Battery Software Suite System
PAtools Battery Software Suite is tailored for EV battery test stations, accommodating various test devices such as battery cells, modules, and packs.
The following are typical components of a single battery test station that uses PAtools Battery Software Suite as a starting point for building a test system.
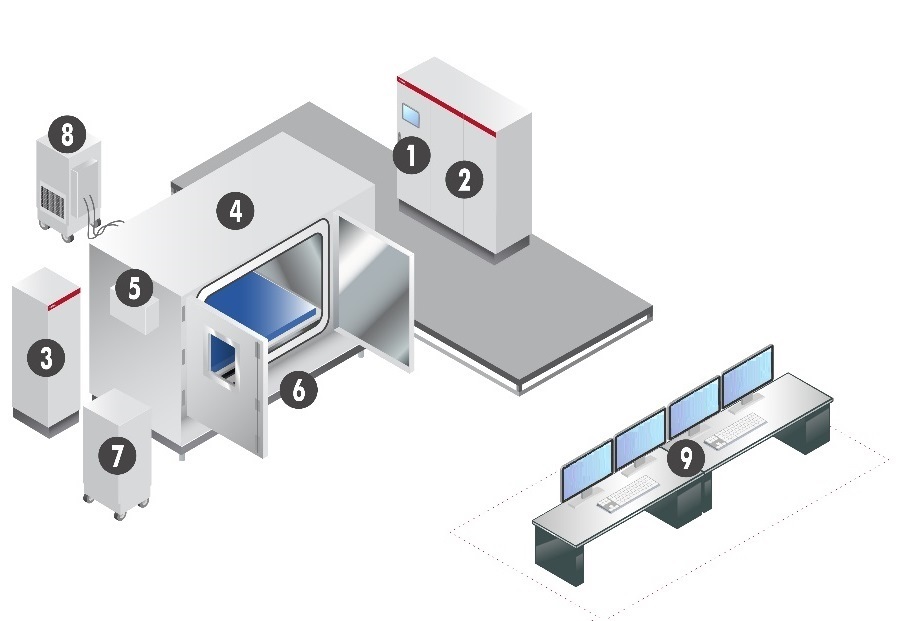
Position | Component | Notes |
---|---|---|
![]() |
DUT |
The device under test. |
1 |
Facility Power Interface |
Provides the power from the facility to the test system. |
2 |
Cycler Cabinet |
Drives charge and discharge cycles of the DUT. |
3 |
Control Cabinet |
Contains the PXI controller that runs the PAtools testing software and other protective electronic components. |
4 |
Climate Chamber |
Encloses a space to enable the manipulation of temperature and humidity conditions during a controlled test. |
5 |
DC Connection Box |
Connects the DUT to the power and measurement equipment. |
6 |
Test Space |
Area where the test occurs. |
7 |
Measurement Rack |
Contains measurement equipment that acquires test data from the DUT. |
8 |
Water Conditioning Unit |
Circulates a liquid coolant to keep the system within acceptable temperatures. |
9 |
Test Monitoring Station |
Provides a location to monitor and interact with the test using SystemLink or PAtools. |
Components of a Modern Battery Lab
The Modern Battery Lab is scalable and includes all components required to perform battery validation tests on a mass scale.
Modern Battery Lab Workflow
There are several roles that participate in the Modern Battery Lab workflow. Depending on the lab, some of these roles may be performed by the same person or split between multiple people.