Manual Testing
Although manual battery testing is a legacy method, it is still used today. Testing a battery manually involves two independent test setups to cycle the same battery. Charging requires connecting the battery to a DC source and discharging requires connecting the battery to a physical resistor. Furthermore, a number of external pieces of equipment, such as DMMs, relays, and transducers, are required to take measurements and need to be switched between sourcing and loading. All these instruments must be manually set up, controlled (start/stop), managed independently, and manually recorded by the user.
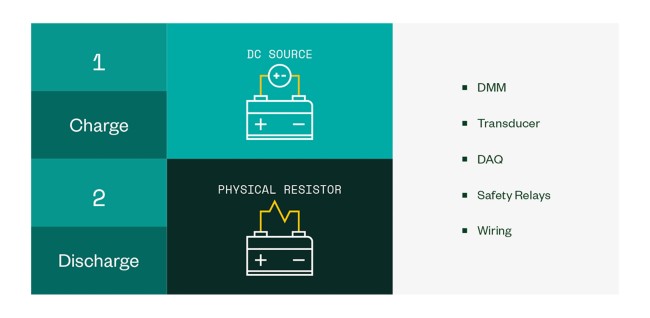
Figure 2: Manual method of battery testing uses two independent set-ups to charge and discharge the battery
Electronic DC Source and DC Load
An approach engineers often take is to build their own battery test setup using an electronic DC source and DC load. These types of general-purpose test equipment are found in most power electronics labs. This approach provides an opportunity to automate testing by programming the test parameters within the source and load. However, these instruments still need to be controlled separately, and external equipment is also required to collect measured data.
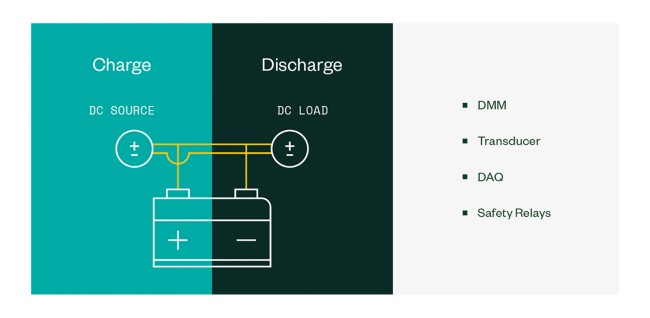
Figure 3: A DC load connected to a DC source battery test set-up is controlled separately and adds complexity
Automated Battery Test Systems
Automated battery test systems integrate an electronic DC source and load within a single product along with advanced built-in automation tools and improved measurement capability. These test systems range from custom-engineered to commercial off-the-shelf (COTS) options. These systems vary in technological approaches, capabilities, and limitations.
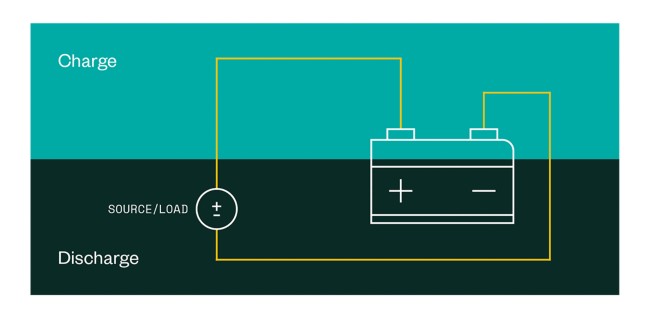
Figure 4: Automated test systems integrate the DC source and load within a single product
Next-Generation Battery Test Systems
Modern battery test systems continue to evolve, providing new capabilities to address changing technology and business needs. Key battery test technology trends include higher voltages for faster charging, wider power ranges, faster response times to emulate real-world conditions of e-mobility, and more environmental testing with broader adoption. On the business side, key trends include declining battery costs, increased use of lithium and alternative materials, shorter design cycles to address increased competition and market growth, and increased outsourcing of testing due to limited talent availability.
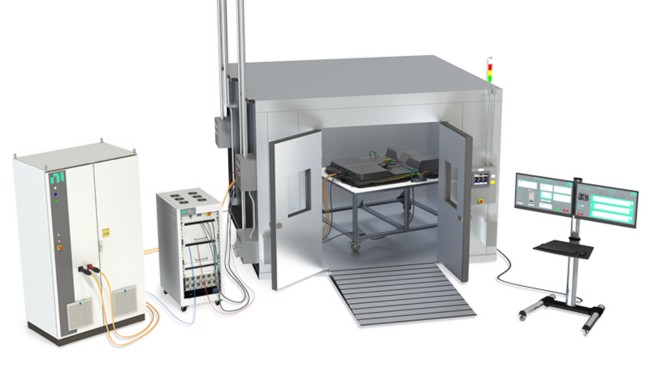
Figure 5: Next generation battery test systems are open, flexible, and can easily integrate with hardware and software to control an entire test environment
To address these trends, battery test systems now require wider operating envelopes (especially voltage and power), modular configurations with scalable and expandable power, multiple layers of integrated safety features, fast transient response times, built-in measurements, and easy third-party integration. To select the right test solution, it’s important to develop a test plan that addresses the technical, user, and business needs of today and in the future. Important elements of a test plan include automation software, battery cycler hardware, and other external equipment including chambers, data acquisition, relays, I/O, and auxiliary loads or sources.
Next-generation battery test solutions provide different options to automate that include multiple programming languages or a powerful test executive that can simplify and reduce software development time and complexity. With respect to hardware, battery cyclers need advanced hardware performance to ensure accurate, scalable, and repeatable test results. Voltage and current transitions, or slew rates, of the test system must be faster than the battery under test to emulate real-world settings. Flexible and scalable power enables users to address future power requirements with no or minimal investment in new infrastructure; having multilayered, built-in safety measures dramatically reduce safety hazards.
Battery test involves more than battery cycling. Users often need the flexibility to have easy integration with third-party tools such as software communication interfaces, temperature chambers, or DAQ systems. Many automated test systems do not easily integrate with third-party tools and as a result, limits testing capability and takes a long time. The ability for a battery test system to interface with and control an entire test environment is critical. Today, data has the power to transform the way companies do business and bring products to market faster. Engineers need to have a connected ecosystem of flexible battery test systems and software automation tools to efficiently test batteries, validate performance and scale testing.
The Benefits of Next-Generation Battery Test Systems
- Reduce time to market and improve engineering productivity
- Decrease capital expenses (CapEx) and operating expenses (OpEx)
- Eliminate use error and ensure repeatable testing
- Reduce safety hazards
- Provide future-proofing to address future power levels